Advanced Wind Turbine Blade Materials: A Sustainable Future
This post contains affiliate links. I may earn a commission at no extra cost to you if you make a purchase. Note that I’m not a health or outdoor safety professional, so further research is advised. Your support keeps Outdoors A-Z running—thank you! Read the full disclosure.. Read the full disclosure here.
Wind energy has emerged as a pivotal player in the global pursuit of sustainable energy solutions. At the heart of harnessing this renewable energy source are wind turbine blades, the unsung heroes silently slicing through the air, converting wind power into electricity. As the wind energy sector continues to expand, the materials used in wind turbine blades have come under intense scrutiny and innovation. The choice of blade materials significantly impacts a turbine’s efficiency, durability, and overall environmental footprint.
In this blog post, we delve into the intricate world of wind turbine blade materials, exploring the evolution from traditional materials like wood and fiberglass to cutting-edge advancements in carbon fiber composites and smart materials. Understanding the nuances of these materials is crucial not only for engineers and scientists pushing the boundaries of wind energy technology but also for consumers and policymakers aiming to embrace sustainable energy alternatives.
Table of Contents
Types of Wind Turbine Blade Materials
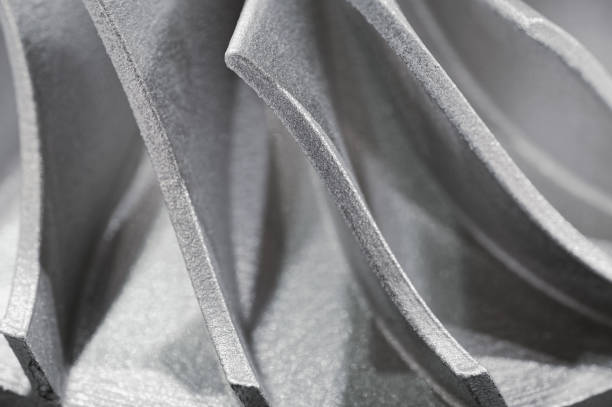
Wind turbine blades have come a long way from their humble beginnings, evolving alongside advancements in materials science and engineering. Understanding the various types of materials used in wind turbine blades is essential to grasp the complexities of this field. Let’s explore the traditional materials that laid the foundation for wind energy technology and the cutting-edge advancements that are shaping the future.
Traditional Materials
Wood
Wood was among the earliest materials used for wind turbine blades. Historically, wooden blades were carved and shaped to catch the wind efficiently. While they are no longer prevalent in large-scale commercial turbines, wooden blades are still used in some small-scale and experimental setups due to their low cost and ease of fabrication.
Fiberglass
Fiberglass-reinforced composites marked a significant leap forward in wind turbine blade technology. Fiberglass blades are lightweight, making them easier to transport and install. These blades are created by layering fiberglass fabric and epoxy resin, resulting in a durable and corrosion-resistant material. Fiberglass blades became popular in the 1980s and are still widely used in smaller wind turbines.
Aluminum
Aluminum blades combine strength with lightweight properties, making them a favorable choice for some mid-sized wind turbines. These blades are often constructed using aluminum alloy sheets or extrusions. While they offer advantages in terms of weight and corrosion resistance, they are not as commonly used in large-scale wind farms due to limitations in size and structural integrity.
Advanced Materials

Carbon Fiber Composites
Carbon fiber composites represent the forefront of wind turbine blade technology. Carbon fiber is incredibly strong and lightweight, making it an ideal material for large turbine blades. These composites are created by weaving carbon fibers into a matrix of epoxy resin, resulting in blades that are not only robust but also highly efficient in capturing wind energy.
Glass Fiber Composites
Glass fiber composites, similar to carbon fiber composites, are made by reinforcing glass fibers with a resin matrix. While not as strong as carbon fiber, glass fiber composites strike a balance between strength, cost, and ease of production. They find applications in various wind turbine sizes and are a popular choice for manufacturers seeking a cost-effective yet reliable solution.
Hybrid Materials
Hybrid materials combine different types of fibers, such as carbon and glass, to harness the strengths of each component. These hybrid composites are engineered to optimize specific properties, such as strength, flexibility, and cost-effectiveness. By blending different materials, engineers can tailor the blade’s composition to meet the demands of specific wind conditions and turbine designs.
Properties of Ideal Wind Turbine Blade Materials

Selecting the right material for wind turbine blades involves a careful consideration of various properties that directly influence the turbine’s performance, longevity, and overall efficiency. An ideal wind turbine blade material should possess a combination of specific characteristics to ensure optimal functionality in the challenging wind energy environment.
Strength and Durability
One of the most crucial properties of wind turbine blade materials is strength. The material must withstand the tremendous forces exerted by strong winds, especially during storms and turbulent weather conditions. Additionally, the material should have excellent fatigue resistance, ensuring that it can endure repeated stress cycles without developing cracks or structural weaknesses. High strength-to-weight ratio is also essential to maintain structural integrity while keeping the overall weight of the turbine blades low.
Weight and Balance
The weight of the turbine blades significantly impacts the turbine’s overall weight and balance. Heavier blades require stronger support structures and foundations, increasing costs and complexity. Lightweight materials, such as carbon fiber composites, offer the advantage of reduced weight without compromising strength. Well-balanced blades are crucial for stable rotation, maximizing energy capture, and minimizing wear and tear on the turbine components.
Fatigue Resistance
Wind turbine blades constantly experience cyclic loading due to wind variations. Fatigue resistance is the material’s ability to endure these cyclical stresses over an extended period without degradation. Blades with high fatigue resistance have a longer operational lifespan, reducing maintenance requirements and downtime. Advanced composites like carbon fiber demonstrate excellent fatigue resistance, making them ideal for large-scale wind turbines.
Cost-effectiveness:
While advanced materials like carbon fiber offer superior properties, their high manufacturing costs can impact the overall affordability of wind turbines. Finding a balance between performance and cost is crucial for the widespread adoption of wind energy technology. Manufacturers often explore innovative manufacturing processes and material combinations to strike the right balance between performance, durability, and cost-effectiveness.
Environmental Impact
The environmental impact of wind turbine blade materials is a growing concern in the renewable energy industry. It’s essential to consider the entire life cycle of the materials, from production to disposal. Sustainable practices, such as recycling and eco-friendly manufacturing processes, play a vital role in reducing the environmental footprint of wind turbine blades. Researchers and engineers are actively exploring ways to make turbine blades more recyclable and environmentally friendly, ensuring that wind energy remains a truly sustainable solution.
Understanding these properties is essential for engineers and researchers working on the design and improvement of wind turbine blades.
Comparison Between Traditional and Advanced Materials
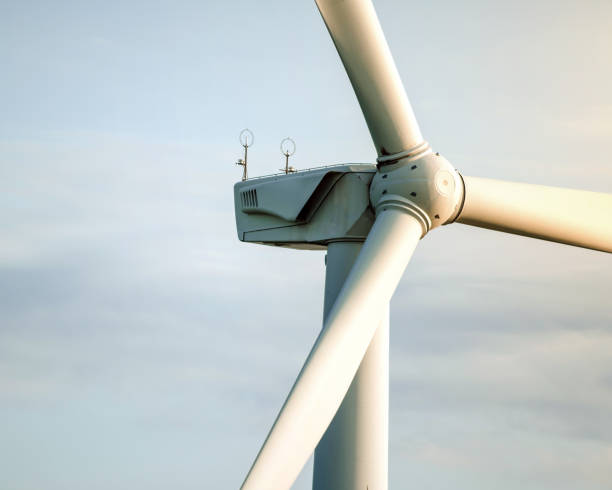
Wind turbine blade materials have traversed a fascinating journey, transitioning from traditional options like wood, fiberglass, and aluminum to the realm of advanced composites such as carbon fiber and glass fiber. Each category of materials comes with its own set of strengths and limitations, influencing the choice of materials in wind turbine design and construction.
Strengths and Weaknesses of Traditional Materials
Wood
Strengths:
- Renewable resource
- Low cost
- Ease of fabrication for small-scale turbines
Weaknesses:
- Limited strength and durability, making it unsuitable for large-scale turbines
- Susceptible to rot and decay, especially in harsh weather conditions
Fiberglass:
Strengths:
- Lightweight and easy to transport
- Corrosion-resistant, ensuring longevity
- Cost-effective for mid-sized turbines
Weaknesses:
- Limited strength compared to advanced composites, restricting use in large turbines
- Prone to damage in severe weather conditions
Aluminum:
Strengths:
- Lightweight and corrosion-resistant
- Relatively low cost
- Suitable for mid-sized turbines
Weaknesses:
- Limited strength for large turbines, leading to size constraints
- Vulnerable to fatigue, impacting long-term durability
Advantages and Challenges of Advanced Materials
Carbon Fiber Composites:
Advantages:
- Exceptional strength-to-weight ratio, allowing for larger and more efficient turbine blades
- High fatigue resistance, ensuring durability and longevity
- Ideal for large-scale turbines, maximizing energy capture
Challenges:
- High manufacturing cost, making it expensive for widespread adoption
- Carbon fiber recycling and disposal methods are still evolving
Glass Fiber Composites:
Advantages:
- Balanced strength, weight, and cost, making them suitable for various turbine sizes
- Durable and corrosion-resistant, reducing maintenance requirements
Challenges:
- Not as strong as carbon fiber, limiting use in the largest turbines
- Limited lifespan compared to carbon fiber, requiring replacements sooner
Hybrid Materials:
Advantages:
- Customizable properties, combining the strengths of different materials
- Enhanced performance tailored to specific wind conditions and turbine designs
Challenges:
- Complexity in manufacturing and optimization, requiring precise engineering
In the ever-evolving landscape of wind energy, researchers and engineers continue to bridge the gap between traditional and advanced materials. Innovative approaches, such as hybrid material combinations and improvements in manufacturing techniques, are addressing the challenges associated with both categories. These advancements pave the way for more efficient, durable, and economically viable wind turbine blades, driving the growth of sustainable energy solutions.
Innovations and Emerging Technologies
Wind turbine blade materials are at the forefront of innovation, driven by a relentless pursuit of efficiency, durability, and sustainability. As the demand for renewable energy grows, researchers and engineers are exploring groundbreaking technologies and materials that push the boundaries of wind energy production.
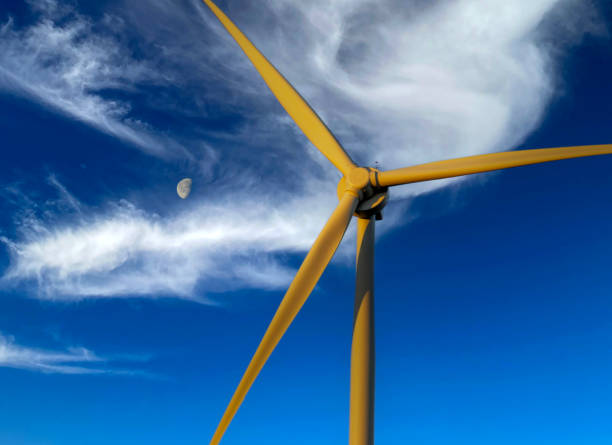
Nanotechnology Applications:
Nanotechnology, the manipulation of materials at the molecular or atomic scale, has opened new avenues in wind turbine blade design. Nanomaterials exhibit extraordinary properties, such as enhanced strength, flexibility, and conductivity.
By incorporating nanocomposites into turbine blades, researchers aim to create materials that are lighter, stronger, and more resistant to wear and fatigue. Additionally, nanotechnology enables the development of advanced coatings that enhance aerodynamic efficiency and reduce drag, optimizing energy capture even further.
Smart Materials and Sensors:
The integration of smart materials and sensors is revolutionizing the way wind turbine blades respond to changing environmental conditions. Smart materials, like shape-memory alloys and piezoelectric materials, can change their properties in response to external stimuli, allowing for adaptive blade designs.
These materials enable blades to adjust their shape and orientation based on wind speed and direction, maximizing energy conversion efficiency. Furthermore, sensors embedded within the blades collect real-time data on structural integrity, stress levels, and environmental factors. This data-driven approach facilitates predictive maintenance, reducing downtime and ensuring the long-term reliability of wind turbines.
3D Printing in Blade Manufacturing:
Additive manufacturing, commonly known as 3D printing, has gained prominence in wind turbine blade manufacturing. 3D printing technology allows for intricate and customized designs, optimizing the aerodynamic profiles of turbine blades. Manufacturers can experiment with complex geometries that were previously challenging to produce, leading to more efficient blade shapes.
Additionally, 3D printing enables the use of novel materials and composites, opening doors to innovative solutions that enhance both performance and sustainability. The rapid prototyping capabilities of 3D printing also accelerate the research and development process, fostering continuous innovation in wind energy technology.
Environmental Considerations
While wind energy is celebrated for its eco-friendly attributes, it’s essential to address the environmental considerations associated with wind turbine blade materials. As the wind energy sector continues to expand, finding sustainable solutions for blade manufacturing, usage, and disposal is paramount to minimize the environmental impact of this renewable energy source.
Recycling and Sustainability Efforts:
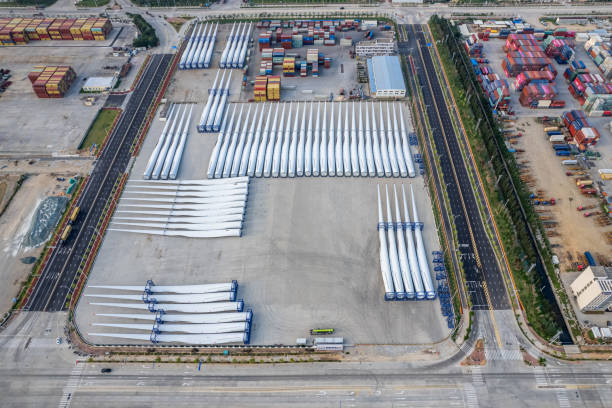
One of the primary challenges in wind turbine blade materials is their end-of-life disposal. Traditional materials like fiberglass pose recycling challenges due to their composite nature. However, researchers and industry experts are actively working on developing recycling methods for composite materials.
Innovative approaches, such as mechanical recycling and chemical processes, are being explored to break down composite materials into reusable components. By investing in research and infrastructure for recycling, the wind energy industry can significantly reduce the environmental footprint of turbine blades.
Life Cycle Analysis of Blade Materials:
Life cycle analysis (LCA) is a comprehensive approach used to assess the environmental impact of wind turbine blade materials from cradle to grave. LCAs consider factors such as raw material extraction, manufacturing processes, transportation, operational lifespan, and end-of-life disposal. By conducting LCAs, researchers and policymakers gain valuable insights into the overall environmental impact of different materials.
These analyses aid in making informed decisions about material selection, allowing the industry to prioritize materials with lower environmental footprints. Additionally, LCAs promote transparency and accountability within the wind energy sector, ensuring that environmental considerations are integrated into the decision-making process.
Addressing the environmental challenges associated with wind turbine blade materials is a collective effort. Collaboration between researchers, manufacturers, policymakers, and environmental organizations is crucial to driving sustainable practices and innovations.
As the industry continues to evolve, a holistic approach to environmental stewardship will be instrumental in securing wind energy’s position as a genuinely sustainable and environmentally friendly energy source.
Future Trends and Challenges
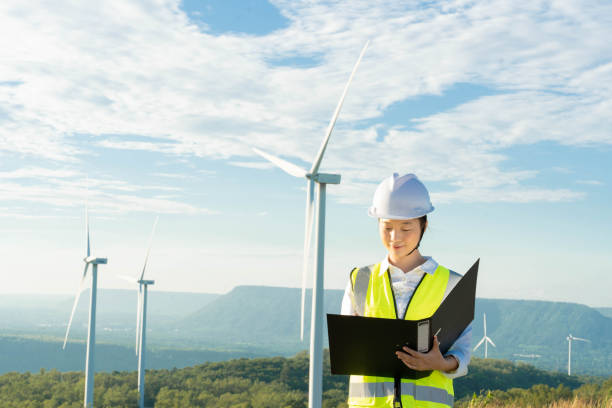
The landscape of wind turbine blade materials is continually evolving, driven by innovation, research breakthroughs, and the pressing need for sustainable energy solutions. Looking ahead, several future trends and challenges are poised to shape the trajectory of wind energy technology.
Anticipated Technological Advancements:
Next-Generation Composite Materials
Researchers are actively exploring advanced composite materials beyond the current options like carbon fiber and glass fiber. Nanocomposites, bio-based polymers, and novel hybrid materials are under scrutiny for their potential to revolutionize blade design. These materials offer the promise of superior strength, enhanced flexibility, and eco-friendly characteristics, setting the stage for more efficient and sustainable wind turbines.
Aerodynamic Innovations
The aerodynamic design of wind turbine blades continues to be a focal point of research. Innovations in blade shape, winglets, and trailing-edge modifications aim to reduce turbulence, enhance energy capture, and increase overall efficiency. Computational simulations and wind tunnel experiments are driving these advancements, enabling precise optimization for various wind conditions.
Regulatory and Environmental Challenges:
Regulatory Frameworks
As wind energy projects expand globally, regulatory frameworks governing the manufacturing, transportation, and installation of turbine blades will need to be standardized and adapted to evolving technologies. Clear guidelines and standards are essential to ensure the safety, reliability, and quality of wind turbine installations across diverse regions and markets.
Environmental Impact Mitigation
Despite progress in recycling technologies, addressing the environmental impact of blade disposal remains a challenge. Research into biodegradable composite materials and sustainable end-of-life solutions is essential. Collaborative efforts between industry stakeholders, recycling facilities, and policymakers are crucial to developing economically viable and environmentally friendly methods for handling decommissioned turbine blades.
Integration of Renewable Energy Systems
The future of energy lies in the integration of renewable sources. Wind energy, when combined with energy storage solutions, smart grid technologies, and complementary renewables like solar power, forms a robust and resilient energy ecosystem. Research into seamless integration methods and energy storage innovations will be pivotal in creating reliable, 24/7 renewable energy systems.
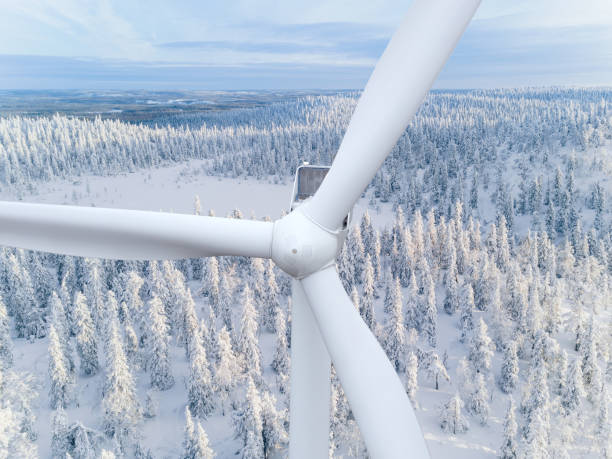
In navigating these future trends and challenges, collaboration between academia, industry, and governments is key. Investment in research and development, international cooperation on standards and best practices, and a commitment to environmental sustainability will collectively drive the wind energy sector toward a greener and more sustainable future.
Conclusion
Wind turbine blade materials have journeyed from traditional origins to the forefront of advanced materials science, reshaping the global energy landscape. As we stand at the intersection of innovation and sustainability, it is imperative to recognize the transformative potential of wind energy and its role in mitigating climate change.
The path forward is paved with challenges, yet it is illuminated by the brilliance of human creativity and determination. By embracing emerging technologies, addressing environmental considerations, and fostering international collaboration, we can propel wind energy to new heights.